Comment: Managing the motor industry’s skills shortage
The motor industry has the sixth highest employment vacancy rate of all sectors. Penny Stoolman, managing director, Prestige Fleet Servicing, outlines actions the industry can take to reduce the impact of the current skills shortage crisis.
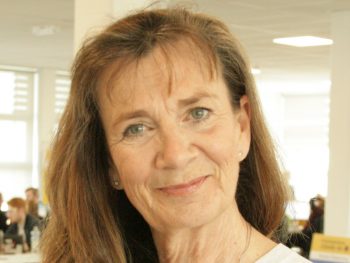
Penny Stoolman, managing director of Prestige Fleet Servicing
The motor industry is facing a perfect storm. That is, when you partner technician skills shortages with the supply chain issues we are currently facing. In fact, when it comes to staff shortages, the motor industry actually has the sixth highest vacancy rate of all UK sectors, with the workshop and technical roles the hardest positions to fill (Autotech Group 2022). So, what are the current bottlenecks when it comes to recruitment and upskilling and how can we solve them?
Post-pandemic disruption is still biting
Being able to hire sufficient mechanics and technicians to perform MOT tests is the biggest worry for 67% of garages, according to recent research by the Motor Ombudsman – a situation thrown into focus by the pandemic. Half of businesses said staff testing positive for Covid-19 or receiving a requirement to self-isolate has caused disruption, while 44% did not have enough staff to handle the new MOTs pattern caused by the MOT exemption. The MOT autumn surge will be in place for at least a decade, according to some industry predictions.
The EV technician shortage issue
Historically, many garages have been one-man bands which close their doors to customers when their owners come to retirement. This is somewhat tricky to say the least in terms of skills retention, especially when you consider the seismic shift in fuel transition that is already underway.
Analysis from the Institute of the Motor Industry (IMI) shows that 90,000 automotive technicians are required to provide the workforce to service the number of EVs on UK roads by 2030, when the Government’s 2030 ICE phase-out deadline kicks in. The IMI believes there will be a shortfall of 35,700 technicians by this point, with 2026 marking the point at which the skills shortfall will start becoming obvious. This will obviously impact businesses longer term as the 2030 ban on petrol and diesel new car sales approaches.
An obvious solution
Investing in young talent is an obvious, cost-effective solution. Nearly two-thirds of businesses have future plans to employ apprentices (Autotech Group, 2022) but there are other avenues to explore. Autotech Academy, launched as a division of Autotech Group in 2021, provides qualified Level 3 automotive students with a gateway into the industry through a paid internship. Working as a conduit between colleges and automotive employers, Autotech Academy screens and equips the intern with a toolbox and uniform. Each internship is customised to suit the employers’ direct needs, ranging from 3-12 months, training with a vehicle manufacturer or equivalent OEM can also be included. Each intern is paid on an hourly basis and, at the end of the internship period, can be employed free of charge by the workshop or garage – it’s effectively a ‘try-before-you-buy’ solution.
It’s an immediate resource solution, as unlike apprentices, interns don’t need day release as they hold all of the theoretical knowledge – they simply need time to gain experience. A ‘grow-your-own’ concept, those who take on an Autotech Academy intern will have, within three to twelve months, a fully qualified, brand-loyal, trained employee.
Invest in training your current team too
Around 40% of garages say they cannot afford the release time to send staff on training courses (Motor Ombudsman, 2022), while 38% also say they are unable to deliver EV servicing. Empty ramps due to resources shortages can equate to thousands of pounds in losses every week. As a result, employing contractors as a temporary solution to plug the skills gap is growing in traction, with a fifth of employers planning to use skilled freelance technicians and MOT testers.
Training, while inconvenient in the short-term, has to be seen as a long-term investment. Ignoring it is a false economy – after all, it’s easier to train existing staff members than to recruit new ones. There are also a number of virtual training courses on offer to learn some key skills that are accessible from anywhere – something well worth considering if ‘day release’ is really not an option for your business.
Shortcutting the shortages – a message for fleets
Essentially, being unable to service a vehicle when it is off the road for repair or requires a service/MOT due to long waiting times as a result of technician shortages is going to cost your fleet money. One way to ensure your fleet servicing, maintenance and repair needs (SMR) are met is to work with a dedicated SMR partner. Working with a partner gives you the tools and transparency to plan ahead – something vitally important when demand has the potential to outstrip supply, both in terms of parts and labour.
Through partnerships such as ours, businesses can also access savings of up to 30% on standard dealership labour rates and parts and all prices are checked for fairness and consistency with our national database. Access to known and predictable monthly costs makes budgeting easier over the whole life of the vehicle, minimising the risk of unexpected high-cost repairs.